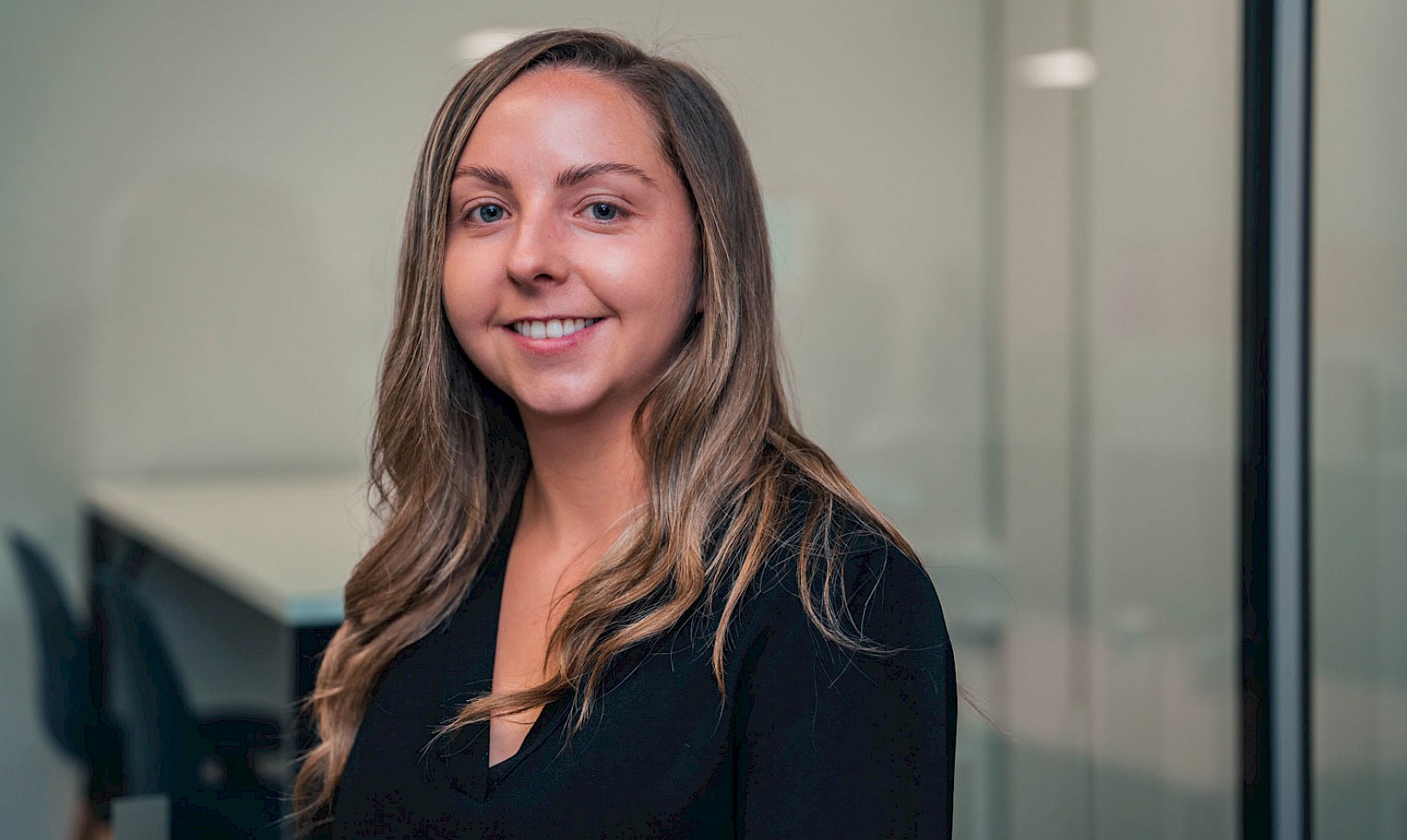
Toxic elements in drug products pose a massive health risk for consumers, resulting in catastrophic reputational damage for producers, as well as huge cost implications. So it’s no surprise that the levels are strictly regulated, and that extensive analysis is available.
We spoke to senior technologist Abby Mills to find out more about the elements we test for.
Q. Where do elemental impurities come from?
Elemental impurities can come from a number of sources. They might be residual impurities that were intentionally added during the formulation. Or impurities present in the drug product or water used in the manufacturing process.
Sometimes they come from the manufacturing equipment itself, or they’ve leached into the drug product from the container closure system.
Q. Can you tell us more about the container closure system?
Leachables can arise in your container closure system for many reasons – such as during the washing and sterilisation stages for example. But studies to understand these leachables will help you ensure the integrity of your container closure system, and mitigate one of the ways elemental impurities might be entering your drug product.
Q. What guidance do you follow when testing for impurities?
Here at Glass Technology Services, we follow the guidance in the ICH Q3D document, which specifies a permissible daily exposure (PDE) limit for a list of 24 elements. The document was created by taking into account various different factors, including human exposure and safety data, administration route and animal studies.
Q. So what does the guidance apply to?
The guidance applies to new finished drug products (as defined in ICH Q6A and Q6B), new drug products containing existing drug substances, and drug products that contain proteins. It doesn’t apply to drug products in clinical stages, herbal products, DNA products or vaccines.
Q. What elements of concern do you look for?
The elements we analyse are grouped into three different classes, which are defined using two factors: the toxicity of the element and the likelihood of occurrence.
Class 1 covers human toxicants – As, Cd, Hg and Pb.
Class 2 covers route-dependent toxicants and is further divided into class 2A and 2B. 2A toxicants (namely Co, Ni, and V) have a high probability of occurrence. As such, a risk assessment is needed across all sources of elemental impurities and routes of administration.
2B elements are less likely to occur unless intentionally added during manufacturing, so they can be removed from the risk assessment. These are Ag, Au, Ir, Os, Pd, Pt, Rh, Ru, Se and Tl.
Class 3 elements have low toxicities if taken orally, but they should be included in the risk assessment if inhaled or taken by parenteral routes. These elements are Ba, Cr, Cu, Li, Mo, Sb and Sn.
PDEs haven’t been established for a number of other elements due to low toxicities and conflicts in regional regulations. But if you’re concerned that they’re present in your drug product, refer to the regional guidelines to ensure you’re performing the correct risk assessment. The elements in this category are Al, B, Ca, Fe, K, Mg, Mn, Na, W and Zn.
Q. How do you perform a risk assessment?
We identify any known or potential elemental impurity, then evaluate it and compare it to the PDE. We then ensure adequate controls are in place during the manufacturing process, and identify any additional controls that are needed to prevent reoccurrence.
Q. How can we find out more?
For an in-depth explanation of the services we offer, visit our pharmaceutical testing and verification page.
You can also download the key takeaways from our three-part webinar series: Pharma glass recalls: Causes and preventative measures. Missed the webinars? Watch the replays.