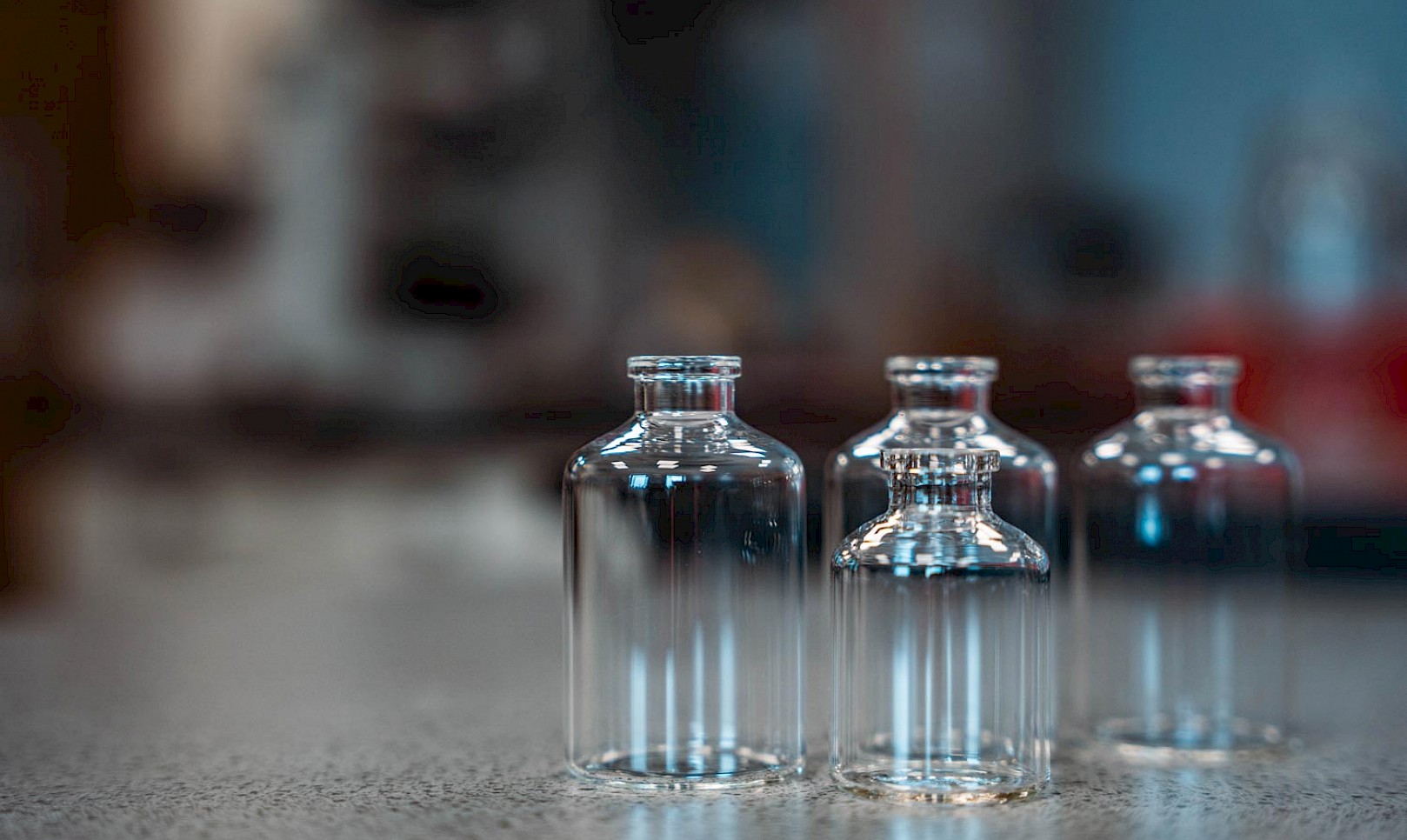
What is the difference between pharmaceutical quality control and quality assurance?
Both quality control and quality assurance are crucial to the success of glass manufacturing for medical products.
Quality control (QC) in the pharmaceutical industry involves identifying product defects through testing and/or inspections. QC tests products in multiple stages of the manufacturing process (from start to finish at regular intervals) to ensure that the customer specifications have been met and documented in compliance with the industry standards. QC is also responsible for recording and escalating out of specification (OOS) events accordingly, and in best practice notifies Quality Assurance and Production of borderline out of specification trends as preventative actions. QC is more intimately connected to the technical understanding of the product and its production. May also be involved with root-cause failure analysis in association with OOS investigations.
Quality assurance (QA), on the other hand, is typically more administrative. QAs are typically responsible for assisting in risk management, document and change control, batch and material releases (especially where risk is associated), audit preparation and accountability, corrective and preventative actions, customer complaints (root-cause failure investigations), compliance training, training documentation, and many other areas (often varied from location to location). This involves preventing mistakes throughout production and managing the quality of finished products by adhering to quality guidelines and high standards.
Every organisation will vary slightly on how much overlap there is between QC and QA. There are also a myriad of other roles for individuals in between these groups that may fall into different categories, the above is not an exhaustive list of everything involved in QA or QC work.
The importance of quality control in the pharmaceutical industry
Quality control in glass fabrication is more than just meeting quality standards. It’s about exceeding them and ensuring that every step of manufacturing is meticulously monitored through testing and/or inspection to guarantee the highest level of safety, performance, and reliability for the final product. Here’s why quality control matters:
Ensures drug safety
Where pharmaceutical products are concerned, safety is critical. Glass packaging should always be durable enough to withstand the acidity or alkalinity of the contents and structurally sound in order to withstand transport and further processing steps (such as Lyophilisation). The glass must meet precise dimensions, thickness, and functional testing in order to work the way it’s intended, protecting the end users (anyone receiving medical care).
Maintains drug efficacy
Glass quality control is so important because the packaging is responsible for holding medications/vaccines/saline. The glass packaging should preserve the sterility of the medication inside, with no faults or weak points. High-quality glass forming can prevent chemical reactions between the drug and the container, avoiding contamination or degradation. So, when glass is manufactured, controlling factors like chemical durability and hydrolytic resistance are monitored in aid to prevent delamination. However, container suitability should be determined per drug product in order to ensure that glass packaging is compatible with the drug and will not cause delamination or compromise the safety or efficacy of the drug. This will also aid in determining shelf life of the drug, ensuring it remains effective until consumed.
Compliance with regulations
There are regulations within the pharmaceutical industry that are there to follow for a reason. Complying with these regulations ensures that medications are manufactured, packaged, and stored as safely as practicable. Glass companies assume the responsibility to make sure their products meet these requirements, as well as implementing risk mitigating factors. Some of the more common regulations for manufacturing of pharmaceutical glass are: USP <660>, USP <790>, ISO 15378 and 9001, BS 1679, Ph. Eur. 3.2.1.
Prevents contamination
It’s so important to prevent defective products from slipping through the cracks of quality assessment. As with any industry, glass packaging should meet quality standards. Ensuring that glass products for the pharma industry are suitable for safely containing and preserving medications is critical to patient safety and preventing contamination. The testing and risk management involved with this process will vary depending on what part of the process it is in. For example, during vial manufacturing primary contamination concerns are aimed at structural integrity, Hydrolytic resistance testing, glass particles, and fused contamination, whereas Ready-to-use (RTU) products will also be looking for endotoxin contamination, sub-visible particles, and any other obvious signs of contamination.
Maintains brand reputation
One flaw in your finished products can risk the company’s image and credibility, as well as risk the patient’s safety. Maintaining your customer’s loyalty by consistently producing high-quality products will only elevate your reputation and help you rise above your competitors. Ensuring end-user safety and customer satisfaction is paramount for pharmaceutical glass manufacturing.
Control processes critical to high-quality glass packaging
Below are some of the most crucial processes to ensure the safety and quality of your glass products. If you want to find out about our processes in more detail, you can read the overview of our glass quality assessments.
Visual inspections
Defects such as cracks, bubbles, inclusions, and chips can lead to compromising sterility, contamination, or interaction with the drug product. By visually inspecting the glass products, most of these faults can be identified and removed from the product line. This process often relies on a combined efforts of human eyes and automated inspection systems equipped with high-resolution cameras and sensors. Using this method ensures that as many of these defects are caught as possible which is critical for patient safety and product quality.
Dimensional measurements and physical testing
It’s important for glass products to be accurate to customer specifications. If not, it could lead to sealing issues or malfunctions during filling or administration, which may affect sterility or dosage accuracy. By checking the dimensions and testing the drug filling process, this can be avoided.
Chemical durability - delamination
Delamination occurs when the inside surface of the glass interacts with the contents causing erosion where silica rich flakes peel off into the product. Testing for hydrolytic resistance (during manufacturing) and additional chemical durability and stability studies (when identifying suitable containers for a given drug) is critical in preventing contamination and ensuring that the glass does not negatively interact with the drug. These tests assist in mitigating risks for delamination in the future.
Thermal shock
Thermal shock testing evaluates the glass's ability to withstand sudden temperature shifts without cracking or breaking. If the glass cracks or breaks, it shows that the product is not to be used until changes are made because it could risk contamination or wastage of glass.
Hydrolytic resistance
In the pharmaceutical industry, many drugs are stored in or as aqueous solutions. Poor hydrolytic resistance can cause glass to release alkali elements into the drug product, resulting in contamination and changes in the drug's pH. This may affect the drug’s stability and efficacy, which is why it’s so important to test glass’ hydrolytic resistance. If the glass breaks down when it’s exposed to water, this is not a good sign!
Risks of inadequate glass control
While there are significant benefits of glass quality control, there are concerns if inadequate control measures are implemented. Here are several:
- Compromised product integrity: Defective glass can lead to container failure, compromised sterility, contamination, and/or interaction with the product.
- Regulatory non-compliance: Failure to meet industry standards can result in legal penalties, recalls, or market withdrawal, affecting company reputation and financial stability.
How Glass Technology Services can help
If you’re searching for a reliable and experienced pharma glass packaging manufacturer, Glass Technology Services is an independent test house and consultancy for the global glass supply chain. Our teams help to resolve production problems, verify the quality of glass packaging and containers, perform container suitability testing, delamination studies, develop innovative glass applications, and more.
We are accredited to ISO/IEC 17025 and ISO 9001 quality standards and have an established reputation for our expertise in glass. By working to these standards, we ensure that we produce the highest quality of glass products we can. You can gain an insight into what services we provide and find out more about our accreditations and memberships here.
From glass failure analysis to delamination and pharmaceutical testing, our glass pharmaceutical services offer a wide range of procedures. You can explore our variety of services specific to the pharmaceutical industry here, and trust that we provide the best experience possible.
If you have a question about what we can offer, or want more information about how we can help your business, please contact our team and we’d be more than happy to answer your questions.
Free webinar: Glass surface durability and delamination
Get access to the webinar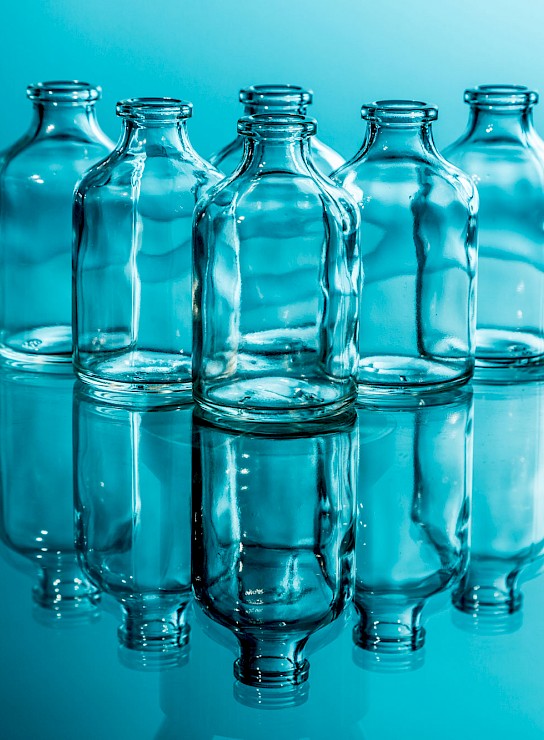