Independent research and development, consultancy and testing facility, Glass Technology Services, looks at developments in product performance testing and says pre-manufacturing assessments are gaining traction across the industry. Catherine Robinson, of our product performance team, explains:
When BBC TV cameras came to our Sheffield laboratories recently, to see our scientists and engineers at work as part of a planned new series on product safety and testing, the production team was visibly amazed at just what toughened glass can withstand.
But physical strength, of course, is only part of the story and our teams are investigating a vast range of product performance testing across all glass sectors and increasingly at pre-installation and pre-manufacturing stages.
Design critique
Consultancy to prepare in-depth design critiques and due diligence data is gaining substantial traction across the glass industry. Performance simulation, by Finite Element Analysis (FEA) is now being used to assess designs - ensuring they are practical, safe and fit-for-purpose and optimising mechanical performance - before mould equipment, tooling and other resources are even considered.
In container and domestic applications, detailed mapping of glass thickness can be carried out to build accurate models with wall thicknesses representative of the final produced items. Simulation models are made using uniform glass distribution in order to first compare the pure design aspects of the product for performance characteristics and then average or worst-case glass thickness distribution variations are calculated to assess their impact upon performance. This enables us to better understand how variances in the thickness of the glass may realistically cause problems in use – and to what extent each design will be affected by expected variations in glass distribution.
For flat and architectural applications, glass thicknesses can be chosen based on deflection and strength, allowing thinner and lighter glass to be used in certain applications. This is of particular use for applications such as shelves, balustrades and showpiece facades where minimal framing is necessary.
Although they do not replace the need for trial runs, these simulations can assess a wide range of expected forces and stresses and take into account specific fixings and frames.
Prevention is better than cure
Testing at the prototype or pilot manufacturing stage can, of course, prevent major expense should a glass product subsequently fail in use, due to design features imparting unintended or unexpected weaknesses which could have been avoided.
Adding potential litigation and compensation costs to product recall charges and also damage to vital company and brand reputation, it is clear to see why the industry recognises that prevention is better than cure.
Design review
In one recent example, a design for a tall, rectangular vase was sent to us for review. We calculated a very high ratio between the size of the base when compared to the height, which whilst giving a striking image, would have caused the vase to be inherently unstable and more likely to fall over.
The design review also revealed that the tight, angular nature of the lower corners would result in high levels of stress forming at the bearing surface during low energy impact - such as if the vase fell over, during packaging or simply washing the item at home.
The bearing surface or standing base of any item is, of course, the area that usually collects the most damage during normal use. Any stresses then applied to this area are more likely to overcome the strength of the weakened glass, resulting in breakage.
We advised either reducing the height of the vase or increasing the footprint of the base, to improve stability, increasing the radii present at the lower edge and creating a thicker standing base region in order to reduce the effects of any induced stress and the potential for breakage.
Failure analysis
In the container glass sector, issues such as broken bottles, wrinkled labels or leaking caps, obviously reflect directly on the brand and have the potential to escalate quickly into significant problems and costs for the brand owner.
Analysing the reason for the failure, tracing it back to the point of origin and taking remedial action to prevent any future issues is crucial.
In one recent case our team received a number of bottles which had broken in use. The failure analysis showed that low energy internal pressure forces had been sufficient to cause breakage from areas of light abrasion damage within the flat face of the bottle.
Given that this was not a natural contact point and the abrasions within this area were very light, the customer was advised that further analysis using FEA may be helpful in understanding the forces applied across the bottle.
Finite Element Analysis - FEA
Simulated internal pressure tests showed that the unique shape of the bottle caused the glass to bend when subjected to internal pressure, creating disproportionally large forces within a small central region of the flat face when compared with other areas of the bottle.
Once this was understood and as a redesign was not an option, because of strong existing awareness of the distinctive brand shape, the customer was able to look into further ways of protecting this susceptible area from damage - for instance by sleeving the bottle.
Process of Elimination
In one case, we were able to show that a number of glass fragments found within two bottles, had been deposited post manufacture, but pre-capping.
Small areas of residual steel material were discovered on the external surfaces of each of the fragments and working with the client were able to assess metal components throughout the filling lines to identify the component that most closely matched the composition of the residential material found on the fragments.
The batch of glass in question was recalled on the grounds of safety and we recommended a full audit of the filling process and a review of their procedure for breakages on line.
Meeting the standards
Standards, specifications and branding requirements continue to increase and tighten across all types of glassware - from drinking glasses, bottles and jars, to flat glass, furniture, pharmaceuticals and specialist glassware.
In the laboratory and on-site, our teams carry out a comprehensive range of testing for a whole range of mechanical, physical, chemical, thermal and optical properties, including impact, thermal shock, internal pressure, vertical load, thermal and solar transmission among many others. Where issues are identified further recommendations and advice can be provided. In the case of specialist or exotic glass, our melting, innovation and research and development departments provide yet further analysis, consultancy and testing support.
The full picture
Computer-simulated assessments are increasingly common throughout the design, trial and production of new products, product modifications and when seeking performance improvements.
Our specialist knowledge in glass properties and performance and extensive experience with manufacturing variations, means that we are able to provide support from initial concept, through manufacturing, distribution and on to end-use.
For glass product designers, manufacturers and specifiers, early-stage intervention and issues analysis is fundamental to their risk management processes.
For our dynamic industry it is also vital protection for the high quality reputation and continued popularity of glass.
Please see www.glass-ts.com or email enquiries@glass-ts.com for further information or support on a whole range of key properties, analyses and testing for the glass and associated industries. Interested readers can also follow us on LinkedIn or subscribe to our new newsletter for regular news, updates and details of our latest R&D projects.
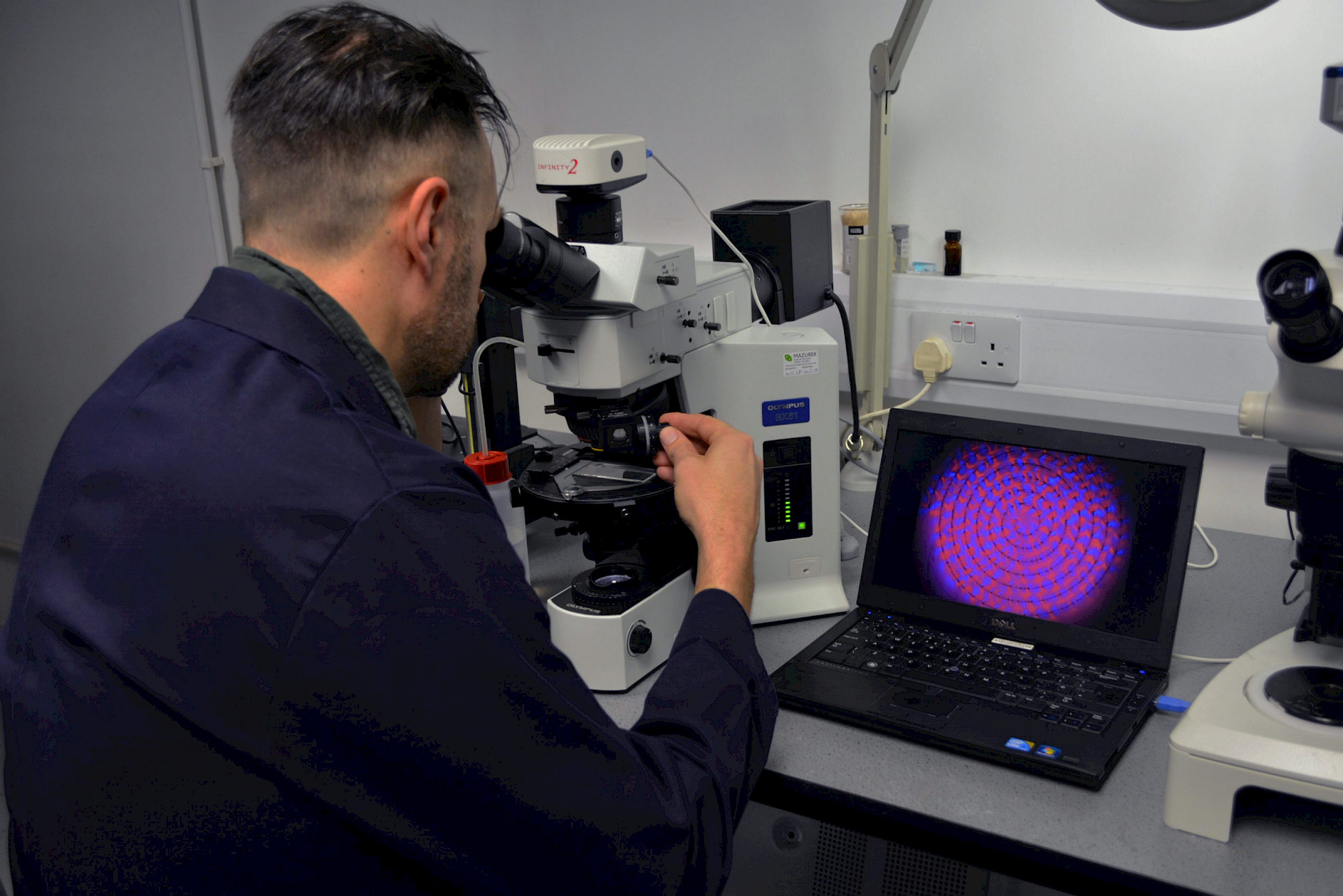
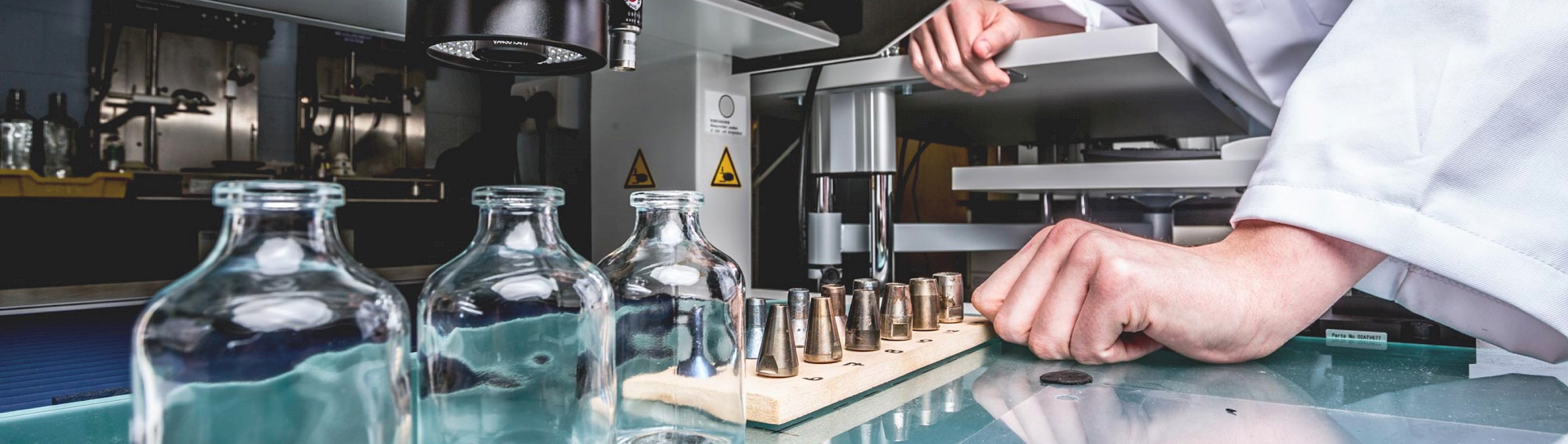